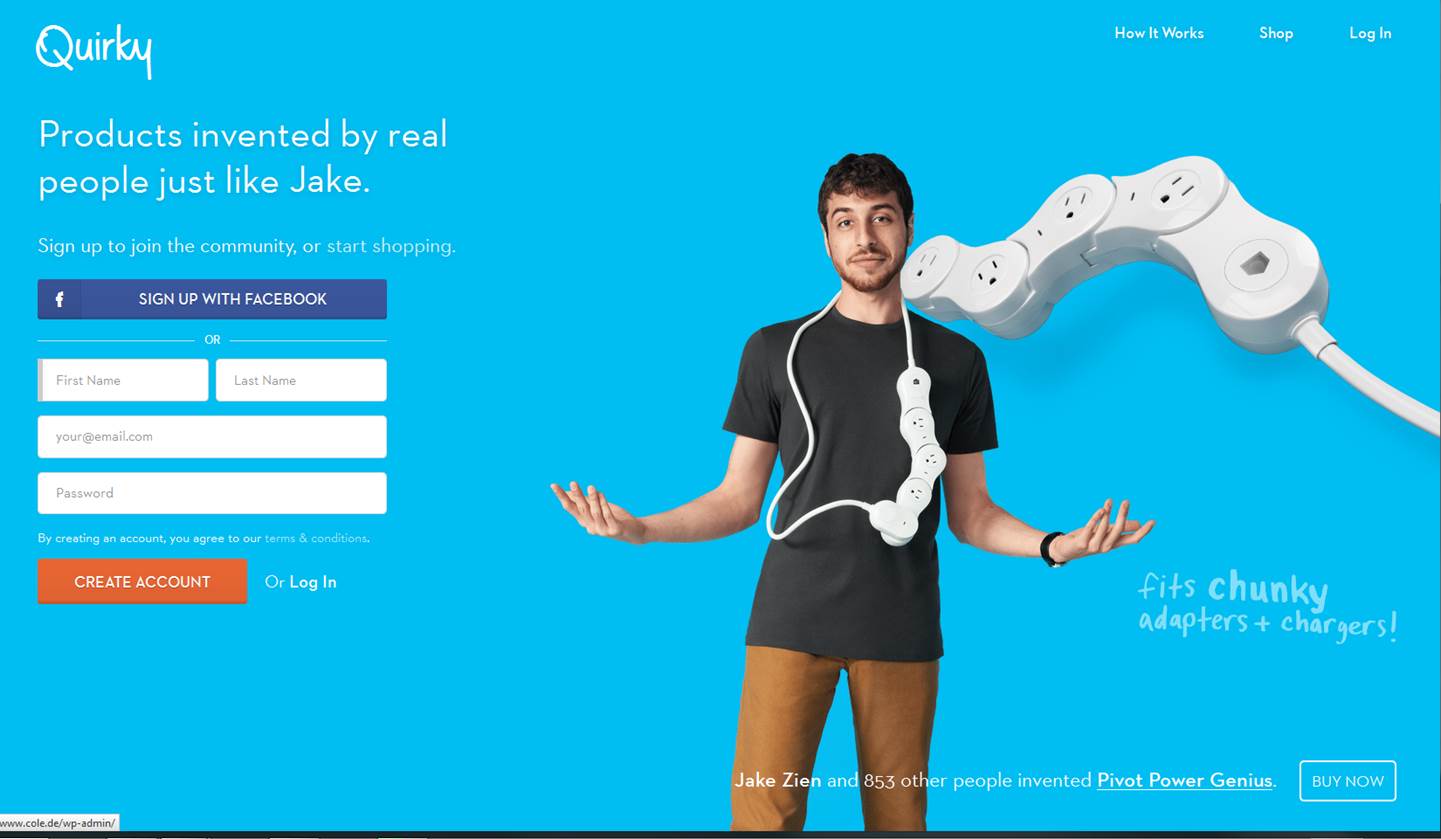
Ist das die Fabrik von morgen?
Das Internet hat die Welt der Wissensarbeit radikal durcheinander gewirbelt. Aber welche Folgen haben Digitalisierung und Vernetzung eigentlich in der Fertigungsindustrie gehabt? Ich muss demnächst auf einer Tagung zum Thema „Industrialisierung 4.0“ reden, und da macht man sich so seine Gedanken…
„Die Rolle der Fertigungsindustrie verändert sich“, schrieben die Analysten von McKinsey im Herbst 2012 in einem Report zum Thema industrielle Globalisierung. Früher bestand der volkswirtschaftliche Beitrag der Produktion vor allem in Wachstumsimpulsen und Beschäftigungszuwachs. Diese Rolle wird sich ändern. In Zukunft wird sie vor allem in Innovation, Produktivitätsverbesserung und Warenaustausch bestehen. Hersteller werden immer mehr Dienstleistungen in Anspruch nehmen und Teilprozesse outsourcen. Dabei werden sie immer abhängiger von globalen Netzwerkeffekten.
Bereits heute sind große Industrie-Konzerne wie Autobauer, Pharmaunternehmen oder Bekleidungshersteller dabei, so genannte „globale Produktionsplattforme“ zu errichten: Fabriken, die jederzeit und blitzschnell umrüstbar sind, um auf kurzfristig wechselnde Anforderungen weltweiter Märkte reagieren zu können. Volkswagen startete 2012 mit seinem MQB-Konzept, was für „Modularer Querbaukasten“ steht. MQB erlaubt, nahezu identische, gewichtsoptimierte Bauteile, die mit neuen hochfesten warmumgeformten Stahlen und Dualphasenstahlen hergestellt werden, in insgesamt 43 Modelle von Audi, Seat, Škoda und Volkswagen sowie zukünftig auch von Volkswagen Nutzfahrzeugen einzubauen. Das System wird in allen VW-Fabriken von Wolfsburg bis Uitenhage, von Changchun bis Chattanooga installiert und soll nicht nur Gewichtsersparnisse von bis zu 60 Kilogramm bringen, sondern VW vor allem in der Fertigung viel flexibler machen als bisher.
Doch als Wachstumsmotor hat die alte „Industrie 1.0“ wohl ausgelebt. Zwar wächst die Fertigungsindustrie global und in absoluten Zahlen betrachtet nach wie vor. Ihr Anteil am Sozialprodukt ist allerdings rückläufig. In Deutschland sank sie von fast 25 Prozent im Jahr 1975 auf weniger als 15 Prozent im Jahr 2010.
Lässt sich dieser Trend dank Digitalisierung umkehren? Beispiele dafür gibt es schon. In Schenectady im US-Bundesstaat New York hat General Electric eine Batteriefabrik gebaut, die in typisch amerikanischer Großspurmanier als die „Fabrik von morgen“ bezeichnet wird. Sie ist mit Tausenden von Sensoren durchzogen, die alles messen von der Temperatur in den Produktionsöfen und dem Energieaufwand, der zur Herstellung jeder einzelnen Batterie nötig ist, bis zur Luftfeuchtigkeit in der Umgebung, weil sie Einfluss auf die Qualität des Endprodukts hat. Steigt der Hygrometer, werden die Einlassöffnungen der Klimaanlage zugemacht, damit weniger feuchte Außenluft in das Ventilationssystem gelangt. Aber General Electric geht noch einen ganzen Schritt weiter – nämlich bis zum Endkunden. Einzelne Batterien für Autos oder Großmaschinen werden ebenfalls mit Sensoren bestückt, die per Internet und WirlessLAN Einsatzdaten an den Hersteller zurückschicken, die zum Beispiel einen Hinweis geben, wenn die Batterie ein Problem hat. GE kann den Kunden rechtzeitig warnen oder einen Kundendienstmitarbeiter vorbeischicken, der die Batterie austauscht, kurz bevor sie den Geist aufgibt.
Jody Markopoulos, CEO der Abteilung GE Intelligent Platforms, sieht die Industrieproduktion durch die globale Vernetzung unter massivem Druck: Die Konkurrenz wächst, die Forderungen der Kunden nach immer individuelleren Produkten ebenfalls, das Tempo des technologischen Wandels nimmt zu. In einer so volatilen Umgebung, so Markopoulos, müssen Hersteller bessere Produkte immer schneller produzieren und auf den Markt bringen, und zwar zu immer niedrigeren Preisen. Effizienzsteigerung ist für sie der einzige Weg zu diesem Ziel – und damit zum Überleben in einer postindustriellen Wirtschaft.
Digitale Vernetzung ist die einzige Lösung, sagt Jody Markopoulos . „Wir müssen die physische Produktion intelligenter machen, indem wir die Maschinen via Software an das Internet anschließen, die Daten aus der Produktion selbst und aus dem Markt auswerten und so neue Erkenntnisse über unsere Arbeit und unsere Produkte gewinnen, um sie zu optimieren und besser zu verkaufen.“
Markolpoulos verwendet den Begriff „Industrial Big Data“ um die Entwicklung zu beschreiben, die sie bereits in vollem Gang sieht und in der es darum geht, möglichst viele Informationen über Menschen, Prozesse und Fertigungsanlagen zusammenzutragen und in Echtzeit auszuwerten. Software wird in einer solchen Produktionsumgebung ständig Trends und Muster auszuwerten haben, um damit Voraussagen über alles vom Maschinenausfall bis hin zu Qualitätsschwankungen zu machen. Vorarbeiter in der Fabrik von morgen werden mit iPads oder Smartphones in der Produktionshalle herumlaufen und blitzschnell auf Warnhinweise reagieren, die von den Fertigungsanlagen ausgesendet werden, und die Maschinen mobil von überall im Werk steuern können – etwa so, wie es heute schon Systemadministratoren in der IT mit ihren Servern machen.
Es tut sich also einiges in den Fabriken der Welt. Aber gleichzeitig ist ein gegenläufiger Trend zu beobachten: Zurück zur guten, alten Manufaktur. Das ist eine Welt sein, in der Einzelne oder kleine Gruppen in der Lage sein werden, die Dinge des täglichen Bedarfes nach gusto zu gestalten und in Eigenarbeit herzustellen, und zwar schneller und billiger als jede Fabrik. Neue Materialien und neuartige Produktionsverfahren wie der genannte 3D-Druck weisen bereits den Weg. Am Horizont erkennbar sind schon Dinge wie persönliche Roboter oder „Collaborative Manufacturing“ – kleine Fertigungskollektive wie Quirky, ein winziges Designstudio, das in einer alten Lagerhalle am Hudson River in New York sitzt und mit Hilfe von 3D-Druckern und Laserschneidern, aber auch ganz konventionellen Drehbänken und Farbsprühern per Internet eingesandte Ideen anderer Leute in greifbare Prototypen verwandelt. „Pivot Power” heißt das bislang erfolgreichste Produkt der vernetzten Manufaktur. Es handelt sich um eine flexible Steckdosenleiste, deren einzelne Sockel so weit auseinander liegen, dass man darin gleichzeitig mehrere klobige Stromadapter einstecken kann, wie sie heute von Laptops, Smartphones und Tablett-PCs benötigt werden. Die Idee stammte von einem Studenten aus Milwaukee, Jake Zien, der inzwischen nach eigenen Angaben über 200.000 Exemplare verkauft und mehrere Hunderttausend Dollar verdient hat.
Quirky erledigt für die Ideengeber solche lästigen Jobs wie Patente anmelden und Bankkredite besorgen. Und über die Online-Community kann Quirky in relativ kurzer Zeit Meinungen von potenziellen Kunden einholen und sagen, ob eine Idee tatsächlich Aussicht darauf haben könnte, als Produkt erfolgreich zu sein.
Ben Kaufman, der Gründer von Quirky, sagte im Interview mit der US-Zeitschrift Forbes, dass kollaborative Manufakturen, wie er sie nennt, für einen entscheidenden Zukunftstrend, weil sie die kollektive Fantasie beflügeln und diese auf völlig neuer Art und Weise in die Realität umsetzen: „Eine Maschine wie ein 3D-Drucker kann theoretisch alles herstellen, was du dir vorstellen kannst – und vieles, was wir uns heute noch gar nicht vorzustellen gewagt haben.“